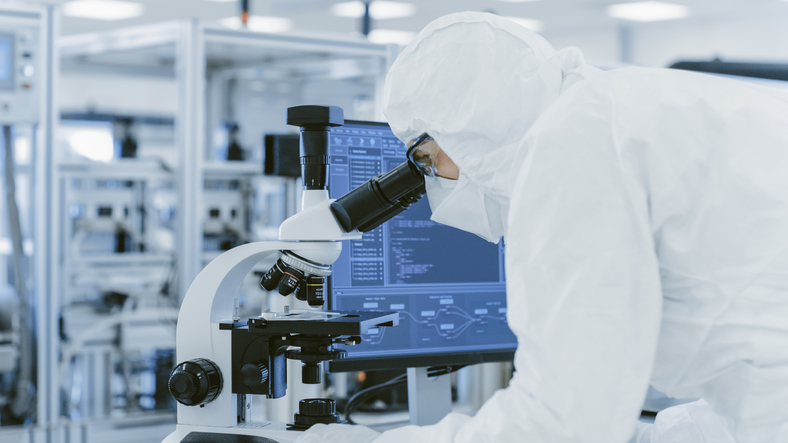
19 Apr 2019 Influences on the quality at paste-free soldering
In our previous article we discussed that paste-free (flux-free) soldering is like cooking. You need the best ingredients and equipment to achieve great results. This article describes the main influences on quality of the soldering results. Nowadays, the flux-free soldering process is an established, high-quality alternative to conventional paste soldering. The process uses preforms (metal sheets) and formic acid or forming gas (N2H2) or pure hydrogen for the reduction of the surface oxides.
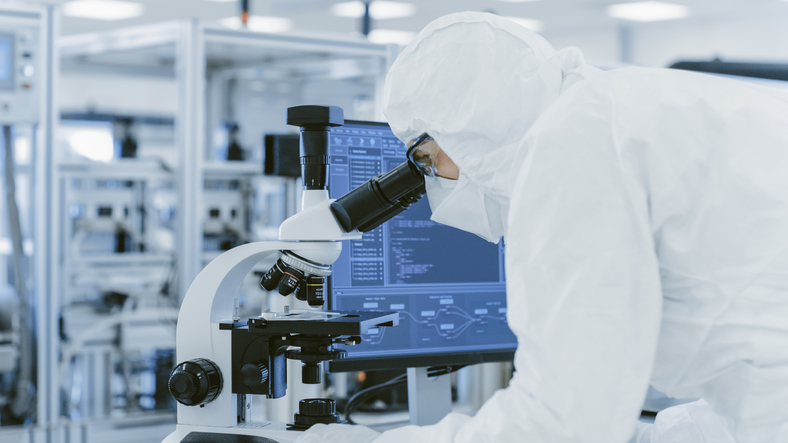
Content of the article
This article discusses the determining factors on flux-free soldering results. Additionally, it proposes solutions that show how these factors can be controlled. The main factors are:
- Material quality
- Temperature profile
- Temperature distribution
- Contamination
- Atmospheres
- Warpage
- Vacuum settings
Overview of the main influences on quality
For the soldering process itself conduction ovens are used (heating by contact). Void-rates below 1% are possible if the boundary conditions are considered. This article highlights the most common failures at paste-free soldering. Figure 1 shows the most common failures, as well as their respective occurence in percent.
Number One: Material quality
The quality of the used materials is the main reason why void-rates below 1% or even below 5% are not achieved. This is especially true for nickel coated devices (e.g. power module baseplates). A variation in layer thickness or different adhesives such as phosphor yields to specific surface properties that influence the wetting of the solder. The coating technique (galvanic or chemical) also has a significant impact on the surface quality. Additionally, storage with exposure to air triggers oxidation processes. These processes are also problematic for preforms, as – depending on the alloy – their shelf live is reduced to 20 minutes when exposed to air. Afterwards, the oxide layer is too thick for the reduction agent to dissolve it completely. Chip metallizations and substrates from established suppliers usually do not cause any issues at soldering. Nevertheless, it is recommended to check their wetting behaviour as well. All materials should always be vacuum sealed. After opening a package, the material should be stored in a drying storage system and be used as soon as possible.
Figure 1: Influencing factors on the quality of solder joints at flux-free soldering without paste.
Temperature profile
The second most common cause for poor soldering results is the temperature profile. At flux-free soldering, the temperature of the reduction medium must be very precisely set. Formic acid works best at 180°C / 356°F. At a too low temperature, no reduction of oxides occurs, whereas a too high temperature leads to a dissolution of formic acid without any surface cleaning. Other important points are the heating and cooling slopes. If the heating rate is too fast, heavy warpage of the products can occur, which results in a (huge) temperature inhomogeneity within the products. Too steep cooling rates may cause shrinkage voids and cracks. The time above the liquidus is relevant for the formation of intermetallic compounds at the interfaces. If this time is too long, heavy intermetallic growth can result and cause a brittle solder layer. Figure 2 shows an example of a typical temperature profile for formic acid soldering.
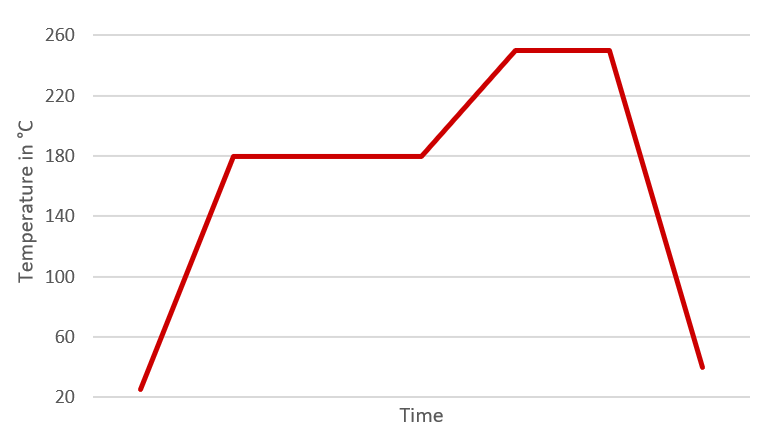
Figure 2: Example for a soldering profile with formic acid and SAC solders.
Temperature distribution
Fast heating gradients (>3 K/s) and the usage of fixtures (soldering jigs) can cause a high temperature gradient within the products (>10 K). As a result, the effect of the formic acid reduction will differ on the product surfaces. Additionally, the temperature above liquidus can no longer be ensured at all parts of the product. So-called cold solder joints can occur or the wettability of the materials will be reduced.
Even at low heating rates (<1 K/s), an inhomogeneous temperature distribution due to a heavy thermal mass of the fixtures and jigs can occur. Thus, choosing an adequate material is essential. The thermal conductivity should be high, whereas the thermal capacity should be very low for the fixtures. Therefore, steel is not appropriate as a jig. Aluminum or titan is a much better choice. For example, 1.2344 steel has a thermal conductivity of 23 W/mK, whereas pure aluminum has a conductivity of 230 W/mK. Further criteria, such as toughness, should also be considered. However, the focus should not only be on the handling.
Another reason for a high temperature gradient within the products is the warpage of the single components. For example, many substrates deform when heated due to the different CTEs. The resulting warpages cause insufficient thermal conductivity between the hot plate and the soldering material. This has to be compensated by soldering jigs or downholders. Figure 3 shows two products on a hot plate. The left sample shows a heavy temperature inhomogeneity due to warpage, while the right product is properly heated due to its flatness.
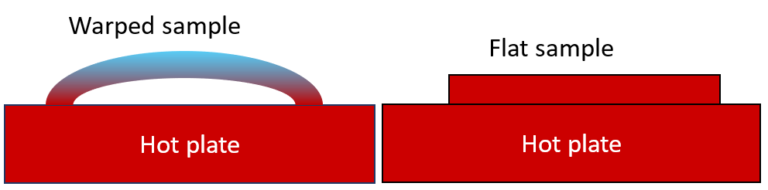
Figure 3: Left: poor thermal conduction due to warpage of the sample; right: good thermal conduction due to flat product.
Warpage
Heavy warpage of the devices can result in solder splashing. Depending on the direction of warpage (concave or convex), gas inclusion within the solder can occur. If these inclusions are removed by vacuum, splashing is highly likely. Therefore, controlling the warpage can prevent solder splashes.
Contamination
Contamination within the soldering chamber are a serious problem for flux-free soldering processes. Formic acid can only remove oxides. If the oxides are covered by impurities (grease, salt, etc.), no cleaning of the surface will occur and the result in a bad wetting of the solder, as well as a high void rate. Therefore, the interfaces need to be clean. This also applies to the walls of the oven chambers. A mixed process of pastes and paste-free processes must be avoided at all costs. Inscriptions with markers on fixtures are also not recommended. The decomposition of the inscriptions can condense on the surface of the products and influence the soldering quality. Also dust or dirt has to be prevented, as the thermal conductivity between hot plate and product will be negatively influenced.
Atmosphere
The atmosphere within the oven chamber is crucial for the quality of the solder joint. Both the oxygen content and the formic acid concentration are influencing the soldering result. The formic acid concentration depends on various factors, such as geometry and fluid level of the bubbler. An oxygen content of >5ppm influences the wetting behavior of the solder significantly, and the reduction impact of the formic acid will be reduced. Therefore, a low leakage rate of the chamber and the pipes is necessary. However, the supply pipe of the formic acid must ensure a constant concentration and be free of oxygen. Consequently, to achieve steady state conditions, empty runs without any product should be performed before starting the soldering process. Video 1 shows the impact of formic acid during soldering.
Video 1: Soldering without and with formic acid., source: Youtube
Vacuum settings and further discussion
In many cases, the vacuum settings are used excessively to improve the void rate. However, other influences are likely the root cause for bad soldering results. With the right vacuum settings, such as power or position of the pipe within the chamber, solder splashes can be avoided. The duration of the vacuum step is often crucial for the void rate.
Conclusion
The flux-free soldering with formic acid and preforms is a special process to achieve high-quality joints. Compared to paste soldering, some important factors have to be considered. The above mentioned factors depict only a small selection of influencing factors.
Literature:
- W.Lin, Y. Lee: Study of fluxless soldering using formic acid vapor, IEEE Transactions on Advanced Packaging ( Volume: 22 , Issue: 4 , Nov 1999 )
- Y. Lin, C. Shih, W. Chang: Fluxless reflow of eutectic solder bump using formic acid, Proceedings of the 2009 12th International Symposium on Integrated Circuits
- A. Hans, G. Elger: Residual free solder process for fluxless solder pastes, 2017 21st European Microelectronics and Packaging Conference (EMPC) & Exhibition
- M. Monta et. al.: Formation of solder cap on Cu pillar bump using formic acid reduction, 2012 IEEE 14th Electronics Packaging Technology Conference (EPTC)
- R. Behera: Development of Fluxless Reflow Soldering Process for Reliable Attachment of Dice for Space Applications, International Journal of Pure and Applied Mathematics, Volume 118 No. 16 2018, 1433-1444
Do you have further questions about vacuum soldering? Contact us today.