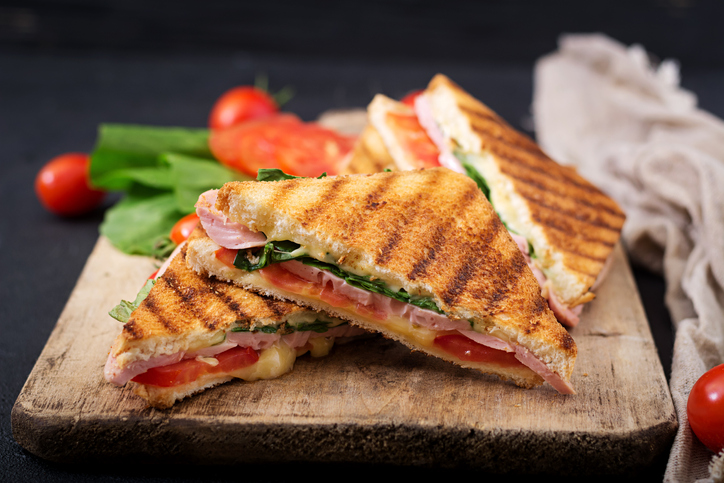
17 Apr 2019 Metallic sintering is like high-end baking
Metallic sintering with silver or copper pastes to attach semiconductor dies, baseplates or coolers has replaced conventional soldering techniques within high-temperature applications. Devices with special requirements regarding lifetime and reliability include the sintering interconnects as well. For a better understanding of the sintering process, the comparison with baking is suitable. The preparation of the paste, the temperature and processing is quite similar to baking a pizza or a sandwich.
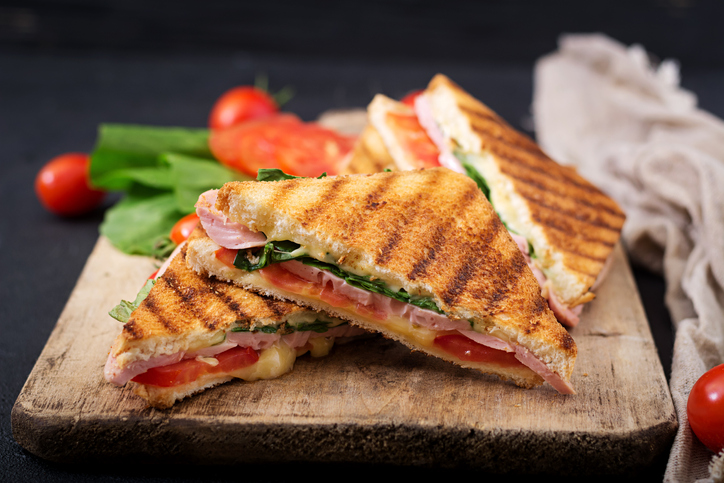
Sintering and baking process flows
The process steps of both manufacturing techniques are comparable. This includes:
- Applying the paste or dough
- Predrying the paste
- Pick&place of components or ingredients
- Final baking or sintering of the product
Step 1: Applying the paste
When baking (or sintering) you generally start with a base. For the pizza, that would be the dough. When you are sintering, it is the paste. The base must be applied on the baking tray (interconnect device) by rolling out or printing. A homogeneous thickness of the paste is important for a good quality (lifetime and reliability) of the end product. Instant products (sintering preforms) can be used as well.
Step 2: Drying
Special doughs need a pre-drying process. For sintering, this is a state-of-the-art procedure. Circulating air ovens dry the paste at temperatures between 60°C and 150°C. If the product is dried for too long, cracks will occur within the layer later. On the other hand, if the drying process is not long enough, unwanted liquids will remain within the interconnect later. The paste will be too soft and drying channels will occur will have a negative influence on the lifetime of the electronic component.
Step3: Pick&Place
After the drying process, ingredients such as lettuce or bacon (semiconductor devices) can be added (to the base). The pressing force is important as devices should neither be damaged from too much force, nor should components shift due to too little pressure.
Baking without pressure
After die placing, the baking procedure follows. It can be pressure-less or pressure-assisted, if further densification is desired. During the pressure-less process the devices will be placed in an oven and a temperature profile will be applied. The process time can last from justa few minutes up to several hours.
Baking with pressure
Compared to pressure-less sintering, the pressure-assisted sintering process has a lot of advantages. The main argument for pressure is the fast process time of a few seconds to a few minutes. Therefore, the pressure-assed process is more commonly used. The principle can be compared to a sandwich maker. Pre-heated plates apply force on both sides of the product and heat up the components within seconds. The higher the pressure, the faster the product heats up. If the force is too high, the devices will be damaged (cheese squeezes out of the sandwich maker). However, if the temperature is too high, the sandwich will burn.
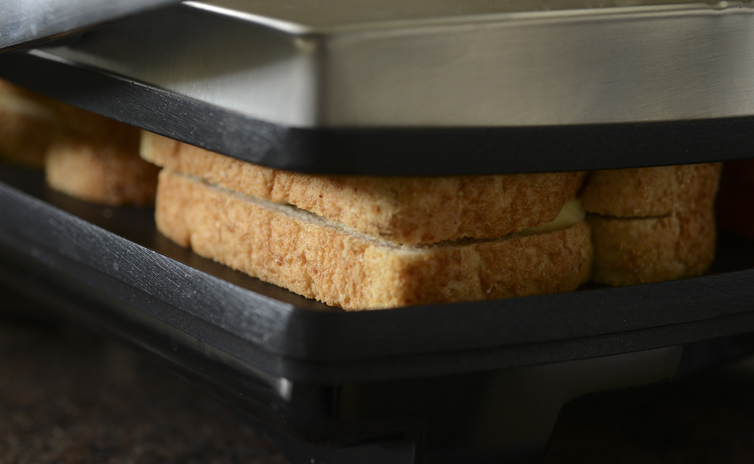
What process engineers can learn from bakers
Similar to award winning bakers, the success of the sintering process depends significantly on the used materials and tools:
- Only fresh ingredients lead to success: Over-stored (rotten) materials must be avoided
- With the best ingredients you can achieve the best results for your customers
- Avoid contamination of the product by wearing gloves.
- Handle with care, especially if the devices are not yet sintered and the paste is still raw. The chips might move and misalign.
- Do not prepare workplaces, refurbish tools or perform other “dirty” activities right next to the sintering line. Or do you clean a dirty baking sheet and the salat for dinner together?
- Only use clean tools! How good can the sandwich be, if old cheese is sticking on the spatula?
- Be focused on a careful preparation: Especially at silver sintering, the previous processes must fit. This includes the printing and drying of paste, as well as the pick&place of devices. A badly rolled pizza dough will burn in some places while still being raw in others.
- Every hair in the soup bothers your guest (creates voids in the interconnect): A cleanroom with special preparations is mandatory for sintering. Compared to soldering, the requirements for cleanroom classes, employee training, cleaning intervals, etc. are much higher.
- Baking time instructions must be followed. Incautious acceleration of the time leads to low quality. The product is burned on the outside but raw on the inside.
- The product temperature is critical for success. Everybody knows the problem: You have a new oven and your recipes are no longer working. The reason for this is that the temperature profile of the new oven differs from the old. Therefore, always check the product temperature (not oven temperature) and distribution.
- Keep an eye on the atmosphere: For sintering, the atmosphere’s composition (oxygen content, sulfur content, organic outgassing) is crucial for success. If you place a glass of water in the oven, the bread will get crunchy and tasteful. If you have remains of cleaning agents in the oven, the bread will be horrible.
- Watch the cooling processes: Cooling too quickly can destroy glasses. If the cooling takes too long, however, your guests will be in a bad mood. Nobody wants to wait long for their meal!
- Keep the storage conditions in mind: The sandwich might have been delicious when it was freshly prepared. But after storing it for two hours at a too high temperature, it will be soft and disgusting.
This might also be interesting for you
Conclusion
Attention to detail is just as important for baking, as it is for sintering. This includes well trained employees that have the capacity to focus on details. Just like at flux-free soldering, the material quality is important for the success. In combination with the best equipment, high quality devices with an extraordinary reliability and lifetime are possible.
Do you have questions regarding the metallic sintering? Do not hesitate to contact us.