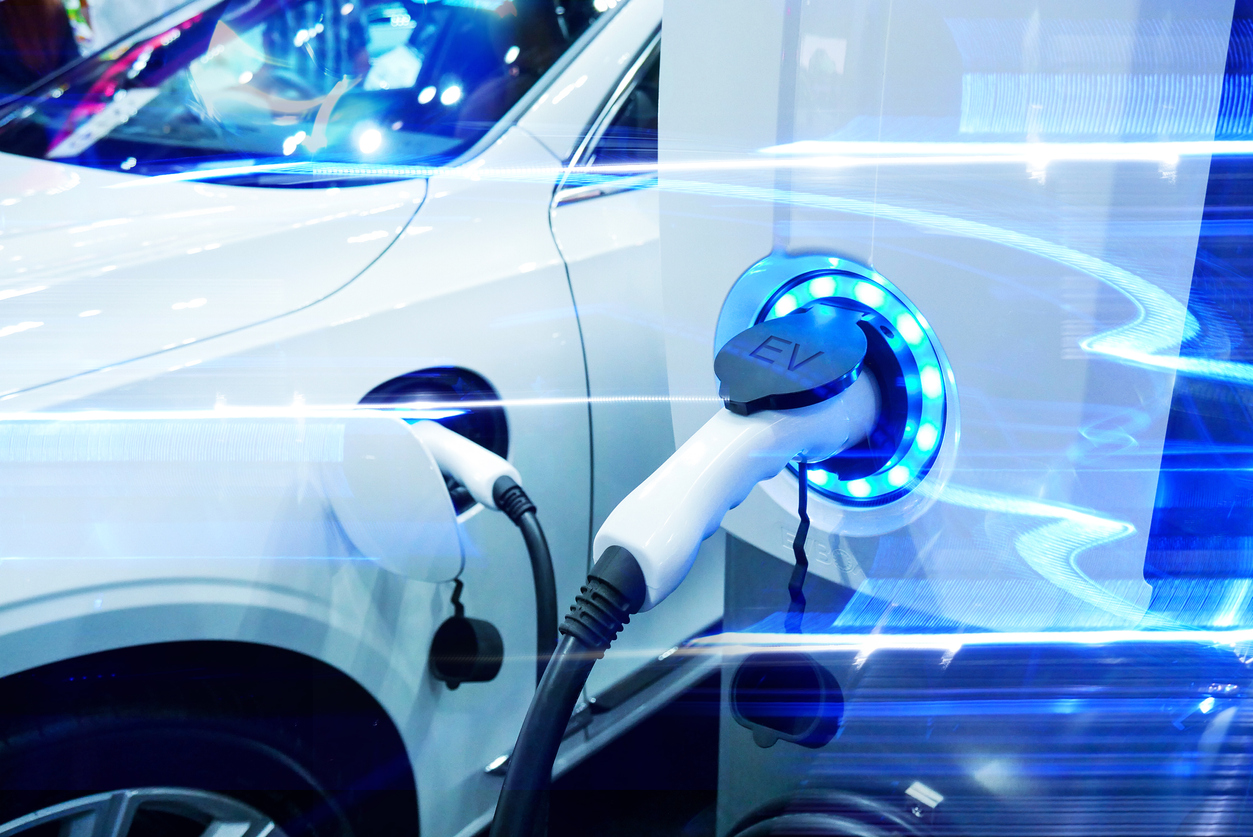
09 Jan 2020 High temperature power cycling tests with sinter / solder materials and SiC devices

Within his Ph.D. thesis, Dr. Aaron Hutzler performed an advanced study on high temperature power cycling with silver sintered interconnects, as well as gold germanium, tin-silver-copper and high lead solders. As test vehicles he used SiC diodes and DBC substrates. From the 480 results he created an easy-to-apply lifetime model for the fast estimation of the field reliability and straightforward design of the maximum dT within power modules.
Realization: Fraunhofer IISB, Department Packaging & Reliability
Ph.D. supervisor: Prof. Martin März (Friedrich-Alexander-University Erlangen-Nuremberg, Department for power electronics)
Further supervisors: Prof. Leo Lorenz (ECPE), Prof. Frank Osterwald (Danfoss Silicon Power)
The present thesis concerns the performance of different die-attach materials for power modules at elevated coolant temperatures up to 120 °C for hybrid electric vehicle applications. The primary focus is on the thermomechanical fatigue of high-temperature packaging technologies at active power cycling tests. With a temperature swing of 130 K, there is a maximum junction temperature of 250 °C. By using 20 samples per run, statistically significant results can be achieved. Simplified test vehicles were selected for power cycling. They comprise of SiC diodes, the die-attach, and a DBC substrate. The topside is connected by aluminum wire bonds with a diameter of 125 µm. For the die-attach, the silver sintering technique is used, as well as Au88Ge12, Pb95Sn5, and SAC305 solder alloys. From the available literature, tin solder is considered a reference. Further reference data was obtained through a survey to create an overview of findings over the last 20 years. In addition, high-temperature results are discussed. Moreover, the power cycling test procedure is analyzed and all available standards reviewed, with special focus on forward-voltage temperature measurement. Power cycling results show higher cycles at increased cooling temperatures. According to state-of-the-art research, this was previously unknown. Tests of the three different empirical lifetime models of power modules showed that material behavior could not be explained by empirical approaches. Therefore, a physical model with temperature-dependent material properties was used as well as the finite element method. To implement plastic material behavior, the toughness modulus of each die-attach material represents a potential solution. In particular, the structure-analytical concept enables fast design recommendations with low computing resources. Thereby, the dimensioning of the power module in terms of maximum temperature swing can be performed. The model considers the geometry of the assembly and the material properties of each layer. Both the physical model and FEM confirmed the observed power cycling results due to decreasing thermo-mechanical stress at elevated temperatures as well as increased ductility of the die-attach materials. This new finding can be used for lifetime modeling and system design of elevated temperature applications. Furthermore, it enables a higher maximum junction temperature of the semiconductor devices, less cooling effort, and increased power density from a packaging perspective.
The thesis is now available as a free download at the Friedrich-Alexander University Erlangen-Nuremberg.