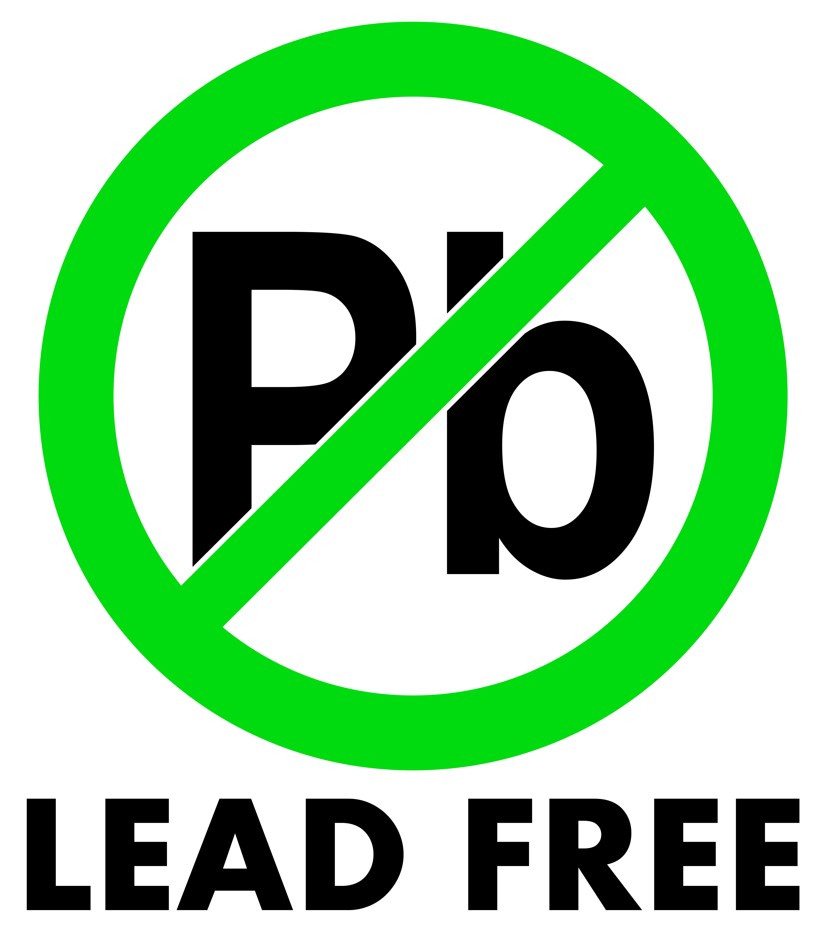
16 Aug 2023 Discovering Alternatives for High Lead Solders in Electronics
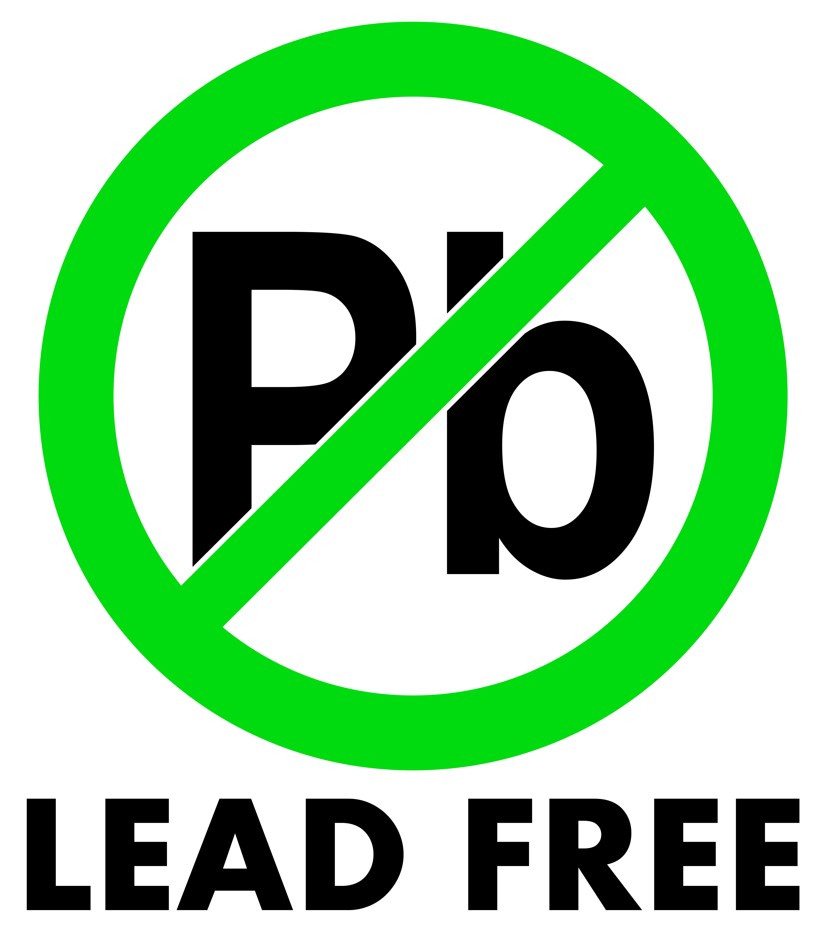
What would happen, if the high lead exemption would end tomorrow?
This article discusses the high-lead exemption for electronics, potential alternatives and what would happen if manufactures had to replace Pb. It will give you an overview of the complex topics and provide further links to do your own background research.
Important: This article purely focuses on the technical challenge and aspects of the alternatives. It has no intention to do any political lobby work or start any discussion on the directive or its exemptions itself.
Current legislation on high-lead solders
In recent years, environmental regulations have been put in place to limit the use of lead in electrical equipment. The European Union has implemented the Restriction of Hazardous Substances (RoHS) directive, which restricts the use of certain elements in electrical and electronic equipment (EEE). The electronics are divided into the following categories:
- Large household appliances.
- Small household appliances.
- IT and telecommunications equipment.
- Consumer equipment.
- Lighting equipment.
- Electrical and electronic tools.
- Toys, leisure and sports equipment.
- Medical devices.
- Monitoring and control instruments including industrial monitoring and control instruments.
- Automatic dispensers.
- Others not covered by any of the categories above
Restricted materials
The following substances are restricted (maximum allowed concentration by weight) :
- Lead (0,1 %)
- Mercury (0,1 %)
- Cadmium (0,01 %)
- Hexavalent chromium (0,1 %)
- Polybrominated biphenyls (PBB) (0,1 %)
- Polybrominated diphenyl ethers (PBDE) (0,1 %)
Exemptions of RoHs directive
However, there are temporary exemptions to the RoHS Directive that allow the use of restricted substances in certain applications where there are not technically and/or economically feasible alternative solutions.
Annex III Exemption 7(a) refers to solder alloys with 85% by weight or more lead. 7(b) takes into account lead in solders for servers, storage and networking infrastructure.
The further extension of the exemptions will be checked for each category again by the European Commission in July 2024 – depending on industry. The commission may decide to revoke or modify it based on the latest scientific and technical evidence.
Evaluation of exemptions
The European Commission appointed the Oeko-Institut in Germany for the evaluation of exemption from Directive 2011/65/EU (RoHS), listed in Annex III and IV. Their website lists detailed reports regarding the technical evaluation and a list of stakeholder companies that applied for the exemption.
Activities on finding high lead solder alloy alternatives
Worldwide many companies are currently working on finding high lead replacement materials. Besides their internal activities, different consortia are working on collaborative effects. One of these consortia is called “Die-Attach 5” DA5 in Germany. DA5 is continuously checking alternatives to high-lead solders. The latest report can be downloaded here.
Another consortium is called “Test & Measurement Coalition” in Belgium. “Their reports can be downloaded on the website of the European Union.
Which solder alloys are currently used and why
A list of the currently used solders under this exemption is listed in the table below.
Table 1: List of solder alloys with a lead (Pb) content of >85% including liquidus and solidus temperature.
Solidus in °C | Liquidus in °C | |||||||
255 | 245 | 85.0 | Pb | 10.0 | Sb | 5.0 | Sn | |
257 | 243 | 90.0 | Sn | 10.0 | Sb | |||
260 | 252 | 90.0 | Pb | 10.0 | Sb | |||
285 | 239 | 92.0 | Pb | 5.0 | Sn | 3.0 | Sb | |
288 | 183 | 85.0 | Pb | 15.0 | Sn | |||
290 | 267 | 88.0 | Pb | 10.0 | Sn | 2.0 | Ag | |
292 | 90.0 | Pb | 5.0 | Ag | 5.0 | Sn | ||
295 | 252 | 95.0 | Pb | 5.0 | Sb | |||
296 | 287 | 92.5 | Pb | 5.0 | Sn | 2.5 | Ag | |
301 | 296 | 93.5 | Pb | 5.0 | Sn | 1.5 | Ag | |
302 | 275 | 90.0 | Pb | 10.0 | Sn | |||
302 | 275 | 89.5 | Pb | 10.5 | Sn | |||
303 | 303 | 97.5 | Pb | 2.5 | Ag | |||
304 | 299 | 95.5 | Pb | 2.5 | Ag | 2.0 | Sn | |
304 | 93.0 | Pb | 3.0 | Sn | 2.0 | In | ||
309 | 309 | 97.5 | Pb | 1.5 | Ag | 1.0 | Sn | |
310 | 290 | 90.0 | Pb | 5.0 | In | 5.0 | Ag | |
310 | 300 | 92.5 | Pb | 5.0 | In | 2.5 | Ag | |
312 | 308 | 95.0 | Pb | 5.0 | Sn | |||
313 | 300 | 95.0 | Pb | 5.0 | In | |||
313 | 313 | 91.0 | Pb | 4.0 | Sn | 4.0 | Ag | |
315 | 98.0 | Pb | 1.2 | Sb | 0.8 | Ga | ||
320 | 300 | 98.0 | Pb | 2.0 | Sb | |||
322 | 310 | 98.5 | Pb | 1.5 | Sb | |||
327 | 100.0 | Pb | ||||||
364 | 305 | 95.0 | Pb | 5.0 | Ag | |||
365 | 304 | 94.5 | Pb | 5.5 | Ag |
There are several reasons to use these high-lead solder alloys. The main objective is to achieve a melting temperature (liquidus + solidus) higher than 260°C, with a preferred temperature of ~300°C. This temperature is necessary to do the following steps in the production process such as
- A second reflow step of the component onto a PCB board with a peak temperature of ~250°C
- Plastic molding step for electrical isolation with a temperature of ~240°C
- High temperature of application
The re-melting of the first alloy (the high lead) must be avoided. Otherwise, components might move due to liquid metal or the reliability of the components (e.g. due to excessive intermetallic compound formation) might be affected.
Another obvious reason is the application temperature. Some electronic components are used in harsh environments with temperatures above 200°C. Due to creep-fatigue mechanisms, the melting point (liquidus and solidus) should always be at least 60°C higher than the application temperature.
Other reasons that make the high-lead solders unique is their easy wetting to very different surfaces and coating qualities. This enables a broad process window and a stable production with yield rates close to 100%. Even if the supplier quality might have high variations, the process and product will not be affected as the high lead solders can tolerate this without any quality impacts.
Additionally, the melting behavior is important for soldering. Eutectic solders are normally preferred (same solidus and liquidus temperatures) while alloys with a melting range (solidus ≠ liquidus temperature) are more difficult to solder. Between solidus and liquidus the solders might melt differently depending on temperature, surface properties and/or contamination. To achieve a good solder joint, a more uniform temperature is needed in the oven. Some areas in the oven might have a different temperature than other areas. Therefore, the solder might not fully melt or just melt for a short period of time in on oven area, while it will be much longer liquid in another area of the oven. As time above liquidus (TAL) is important for the reliability and lifetime of the solder joint, this might cause a high deviation during the application and will increase the after-sales support costs.
Besides the processing, lifetime and reliability requirements of the electronics must also be fulfilled. In this case, lead provides an outstanding ductility (ability to deform under mechanical stress instead of cracking such as ceramics). During the usage of electronics, they will see a lot of different loads. Temperature changes and drop shocks are some examples. High ductility improves the capability of the materials to withstand these loads. Lead might deform but will not crack due to it’s high ductility.
Finally, lead provides a good resistivity against corrosion (performance in humid environments and oxidation (aging due to oxygen). Especially the resistance against oxidation is important for shipment, storage and shelf life. High lead solders can be used for years while other alloys tend to form oxides within minutes or hours.
Why is it so hard to find alternatives
The unique combination of material properties makes it very difficult to find alternatives for high lead solders. The requirements for the alternatives are:
- Melting temperature between 260 and 320..360°C
- Good wetting properties
- For nickel surfaces: Sn content <3% to avoid Ni leaching / dealloying
- Ductility of 20…200%
- Equal corrosion and oxidation resistivity
- Equal thermal and electrical conductivity
- Similar pricing
In terms of solder alloys, the list below shows state-of-the-art solder lead-free alloys with a melting temperature between 250 and 360°C.
Table 2: Review of alternatives
Solidus in °C | Liquidus in °C | |||||
257 | 243 | 90.0 | Sn | 10.0 | Sb | |
266 | 266 | 82.6 | Cd | 17.4 | Zn | |
271 | 100.0 | Bi | ||||
280 | 280 | 80.0 | Au | 20.0 | Sn | |
295 | 221 | 90.0 | Sn | 10.0 | Ag | |
300 | 227 | 97.0 | Sn | 3.0 | Cu | |
330 | 231 | 98.0 | Sn | 2.0 | As | |
345 | 232 | 99.0 | Sn | 1.0 | Ge | |
356 | 356 | 88.0 | Au | 12.0 | Ge | |
360 | 262 | 89.0 | Bi | 11.0 | Ag | |
363 | 363 | 96.8 | Au | 3.2 | Si |
Discussion of lead-free solder alloys
Let’s discuss the alloys listed in table 2. Tin-Antimony SnSb5 and SnSb10 are widely used for substrate to heatsink attaches. As there is no semiconductor chip involved as a joining partner, no leaching is expected. Even though if the Ni of a heatsink, baseplate or water jacked will leach, the impact is normally not that huge, as the metallization is thick enough (>6µm) or there is copper underneath the Nickel. Besides the technical properties of Antimony, it is also on the CoRAP list of the European Union. According to the European Chemicals Agency ECHA CoRAP means: “If a substance is on this list, it means that a Member State has evaluated or will evaluate it over the coming years. The list is called the Community rolling action plan (CoRAP)”. In this context, Sb is suspected to be carcinogenic.
Unfortunately, this alloy cannot be used for any semiconductor die-attach applications due to the dealloying effects. In general, all Sn-based alloys in the list are not useable for thin Au, Ag, or Ni coatings with non-solderable materials underneath such as Aluminum or Titanium.
Another group of the alloys in table 2 consists of Bismuth based solders. Bi is very brittle and therefore needs to be mixed with other elements. So pure bismuth cannot be used for electronics soldering or only for special applications where ductility is not required. Besides ductility Bismuth has a very low thermal conductivity of just 10 W/mK while lead has more than three times higher conductivity with ~35 W/mK. The alloy containing Bismuth (89%)-Silver (11%) has an increased thermal conductivity but also an extreme melting range of 100°C from 262°C to 360°C. Therefore, it is very difficult to solder.
The only alloys left are gold based solders. Due to the high price, these solders are only used in special applications, such as lasers, aerospace or miliary. For consumer or high-volume products, it will not be possible to manufacture electronics economically.
Other alternatives for high-lead solder alloys
In the last years several alternatives have been developed. This includes:
- Metallic sintering with silver or copper and with or without pressure
- Hybrids of metallic sintering particles and epoxy adhesives
- Transfer liquid phase sintering (Diffusion solders)
- New alloy developments
Metallic sintering
A promising alternative to high lead is metallic sintering. In this process silver or copper particles are sintered at 200-300°C absolute temperature. The process can be done with and without pressure. Different variations (e.g. Cu microstructures) as well hybrids consisting of epoxy filled sintering materials are available on the market. The material provides an outstanding reliability (upto 20x increase compared to high-lead) as well as a 10x better thermal- and electrical conductivity.
Why is the industry not already using metallic sintering as a high-lead replacement?
The main disadvantage are the costs. Compared to high-lead solder paste, the sintering material is roughly 20 times more expensive (Cu sintering material) or up to 50 times more expensive (Ag material).
Additionally, due to the missing liquid phase, there is no equalization of process variation. This results in a much higher accuracy needed at the pre-processes such as printing or dispensing.
For pressure sintering there is also a press needed, which results in significant equipment investments.
In contrast, the pressure-less sintering material can be processed with conventional hot air reflow convection ovens. Unfortunately, the typical process time is 30min up to several hours. In comparison, a standard reflow profile for high-lead solders just takes 4-5 minutes.
Concluding, the metallic sintering material can be used as a high-lead replacement, but higher material costs and new equipment investments must be considered. With the ongoing developments, the prices – especially for Cu sintering materials – are expected to drop significantly within the next years as well as process times will be shorter for the pressure-less sintering material.
Transient liquid phase bonding / Diffusion soldering
There are several names and appreciations for the same process:
- Transient liquid phase sintering (TLPS)
- Transient liquid phase bonding (TLPB)
- Diffusion soldering
- Diffusion bonding
The principle is always the same. A solder material consisting of two or more metals form an intermetallic bond that has a higher melting temperature than the material used at the beginning of the process. For example, a copper – tin intermetallic compound has a melting point of 415°C. During the process, Sn melting at 232°C and shaping an intermetallic layer if copper is present. As the diffusion layer and process works only for a few micrometers in thickness within a reasonable soldering time of a few minutes, the layer must be very thin. Layers of 10µm or less and normally smooth or polished surface is required. The material is mass-production proven but requires special equipment to apply a small pressure onto the joint to ensure the formation of the intermetallic.
In conclusion, the TLPS material can be an alternative to high lead. As thin layers and smooth surfaces as well as a pressure of a few grams is needed, it is not an easy drop in solution for Pb solders.
New alloy developments
To successfully replace high lead from electronic devices, the development of new alloys seem to be the best option. Based on the TLPS technology or a mixed alloy technology, a new material might come up that can be used as a drop-in solution for high-lead solders. From a material standpoint, Indium based alloys can achieve the required properties.
A diffusion solder that might be processable below 200°C and remelts at >350°C could also be a solution. Especially when polymers or transfer molds are involved, a melting point below the glass transition temperature of 180…220°C is required not to affect the lifetime and reliability of the polymers.
What would happen, if the high lead exemption would end tomorrow?
The answer to that question is typically engineer-like: it depends!
Are there alternatives to high lead that can be used immediately? yes, but…
- New equipment is needed (e.g. for Ag sintering)
- Process knowledge and trained employees are needed
- Supply chain needs to be adjusted
- More research and development resources need to be assigned to that activity
- Somebody will pay for it!
Would the costs for end-customers and users go up: definitely!
Would certain products not be produced anymore: Unlikely, as long as customers are willing to pay higher prices for the technology change and new materials needed
Would manufacturing companies suffer: every technology change is a challenge and an opportunity. There will be winners and losers for sure
Would it accelerate innovation to find alternatives? Definitely!
Further links:
Do you have further questions about soldering and sintering under controlled atmospheres? Then feel free to contact us.